

To the right is where we left off with the last part of this tutorial. With all the introductory stuff out of the way, it’s time to finish the job. In the first part of this tutorial, we took a look at the idea behind Blender – mesh editing – and how to interact with vertices, edges, and faces to make a thing. Need a part for a mechanical device? Don’t use Blender. Want to model some Greek and Roman statuaries? Blender is a great tool. Want to print out a plastic tree? Blender is a great tool. Blender is a tool for organic and sculptural forms. If you want to make precise mechanical parts, don’t use Blender. In the first part of this tutorial, I said using Blender to create a simple mechanical object like our ‘thing’ is akin to using a bulldozer to build a sandcastle. The Curse of Blender & What We’ve Done So Far It serves our purpose, though: a template with which to make something with a 3D CAD package.īy the way, if anyone out there has a 1st edition of Engineering Drawing, I’d love to see if this object actually goes all the way back to the 1911 volume. Yep, it’s an 85-year-old drawing with fractional inches.
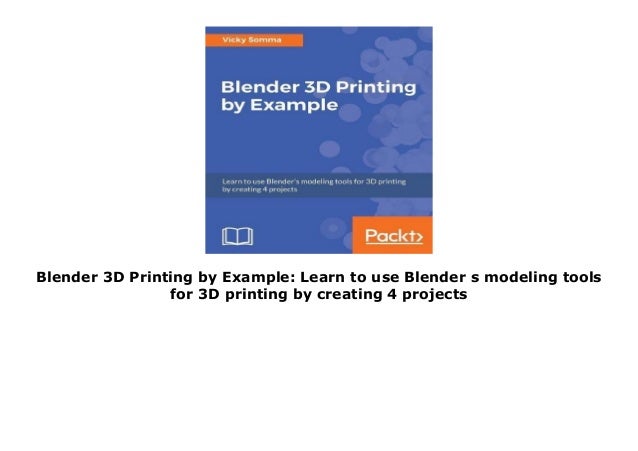
It’s taken out of the 4th edition of Engineering Drawing (French, 1929, p. To the right is the ‘thing’ we’re making for all these 3D Printering tutorials. Check out the rest of the tutorial below. We’ve already done half the work to make a ‘thing’ in Blender, so now it’s time to finish the job. Here’s some links to those other ‘Making a Thing’ posts: Previously, we’ve made the same part in other 3D design packages. In this post, we’re continuing our previous misadventures with Blender by making a ‘thing’ torn from a very old book on drafting. That’s a problem if you don’t know how to create and edit 3D objects.
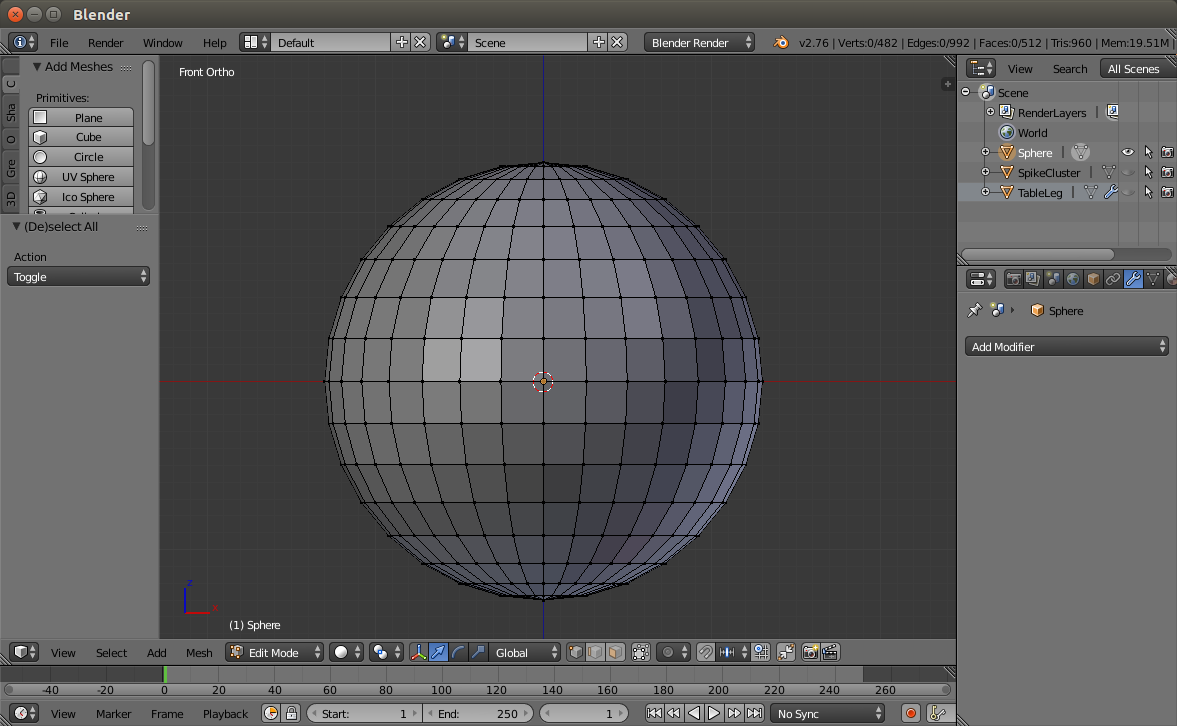
So you have a 3D printer and need to print something of your own design.
